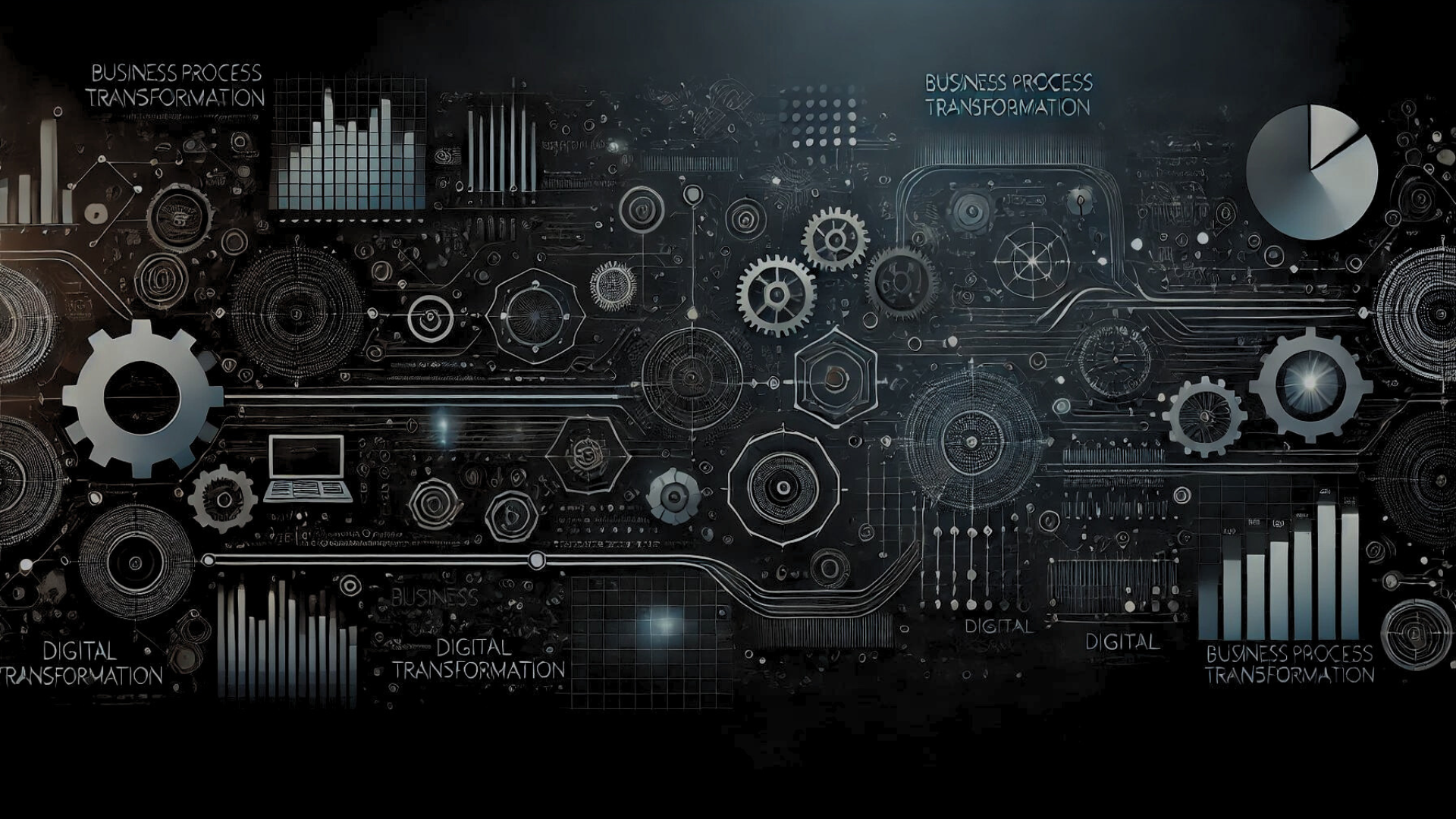
Business Process Transformation
Visualise, optimise, and prepare your process for technology integration
Process Mapping: Enhancing Business Efficiency
‘A good sketch is better than a long speech.’
Often times organisations have an idea of how their processes run, but the reality frequently differs. This is where process mapping comes into play, providing a clear and accurate representation of how it is truly running. By breaking down complex processes into visual diagrams, process mapping serves as a technique to visualise and understand the workflows within an organisation. It provides greater transparency around decision-making, identifies redundancies, and highlights bottlenecks within and between processes.
Why is Process Mapping Important?
A picture is worth a thousand words: by using visual cues and symbols, process maps simplify complex workflows, making them easier to understand for a broad audience. This leads to increased engagement compared to long-form documentation, which can be tedious to create and consume.
Identification of problems: Process maps help teams quickly identify areas of inefficiency, such as redundant steps or bottlenecks, allowing for targeted improvements.
Standardisation and who does what? Mapping processes increases standardisation across the organisation, ensuring everyone is not only aware of their roles and responsibilities but others as well.
Improved Team Performance: Clear processes lead to better team performance, shorter training times, and higher employee satisfaction.
Our Approach to Process Mapping
We specialise in customising process mapping using a wide range of BPMN tools, adapting to your specific requirements and budget.
Our process begins by collaborating with your leadership to identify key process objectives and align them with your business strategy. We then engage with employees who perform the daily tasks, gaining insights into the actual workflow to identify pain points and improvements.
We also assess the system landscape and data flows, ensuring we understand how your current technology supports your operations, enabling us to create accurate and actionable maps that reflect both business needs and the technical environment.
Some Tools We Use
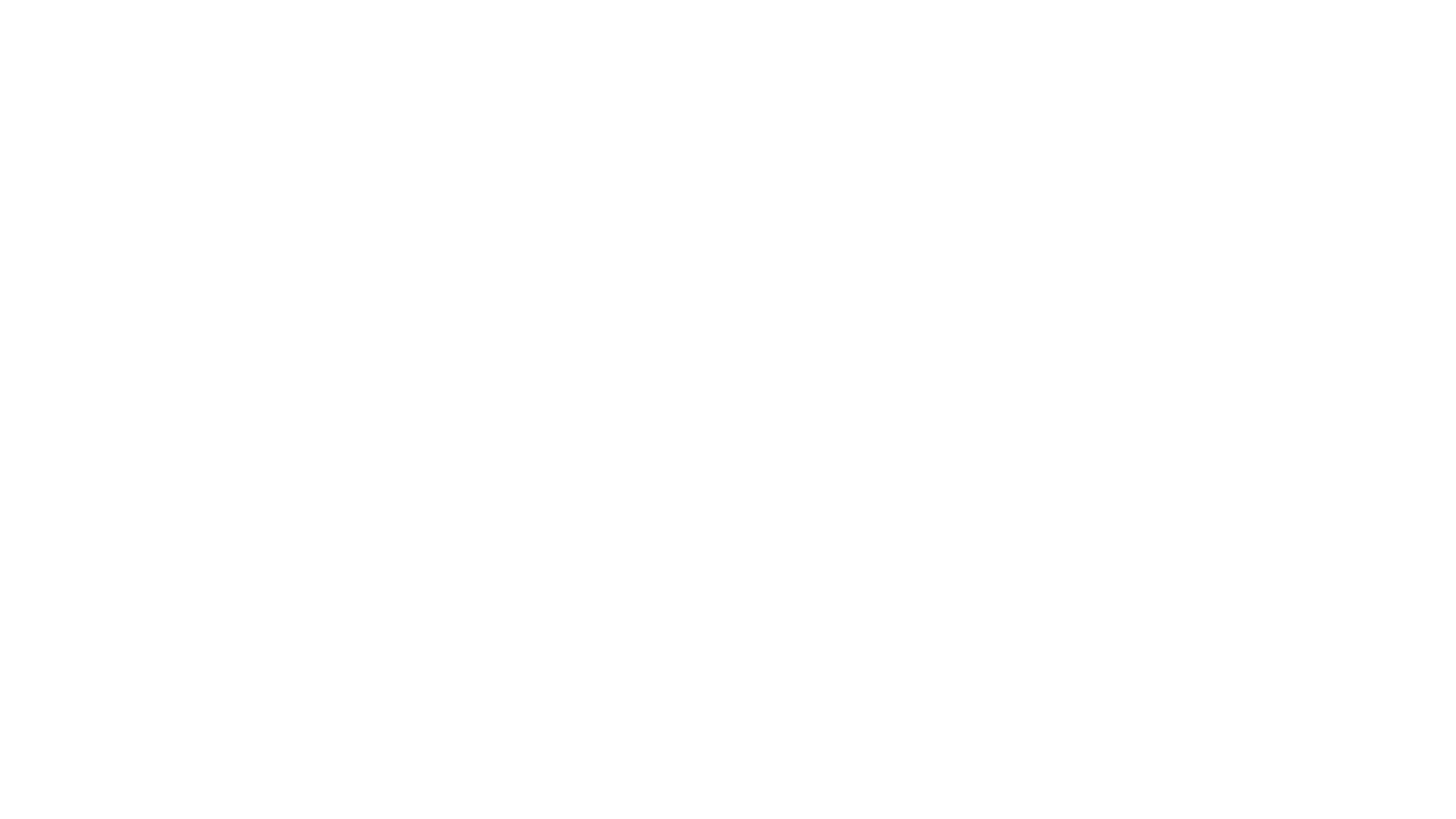
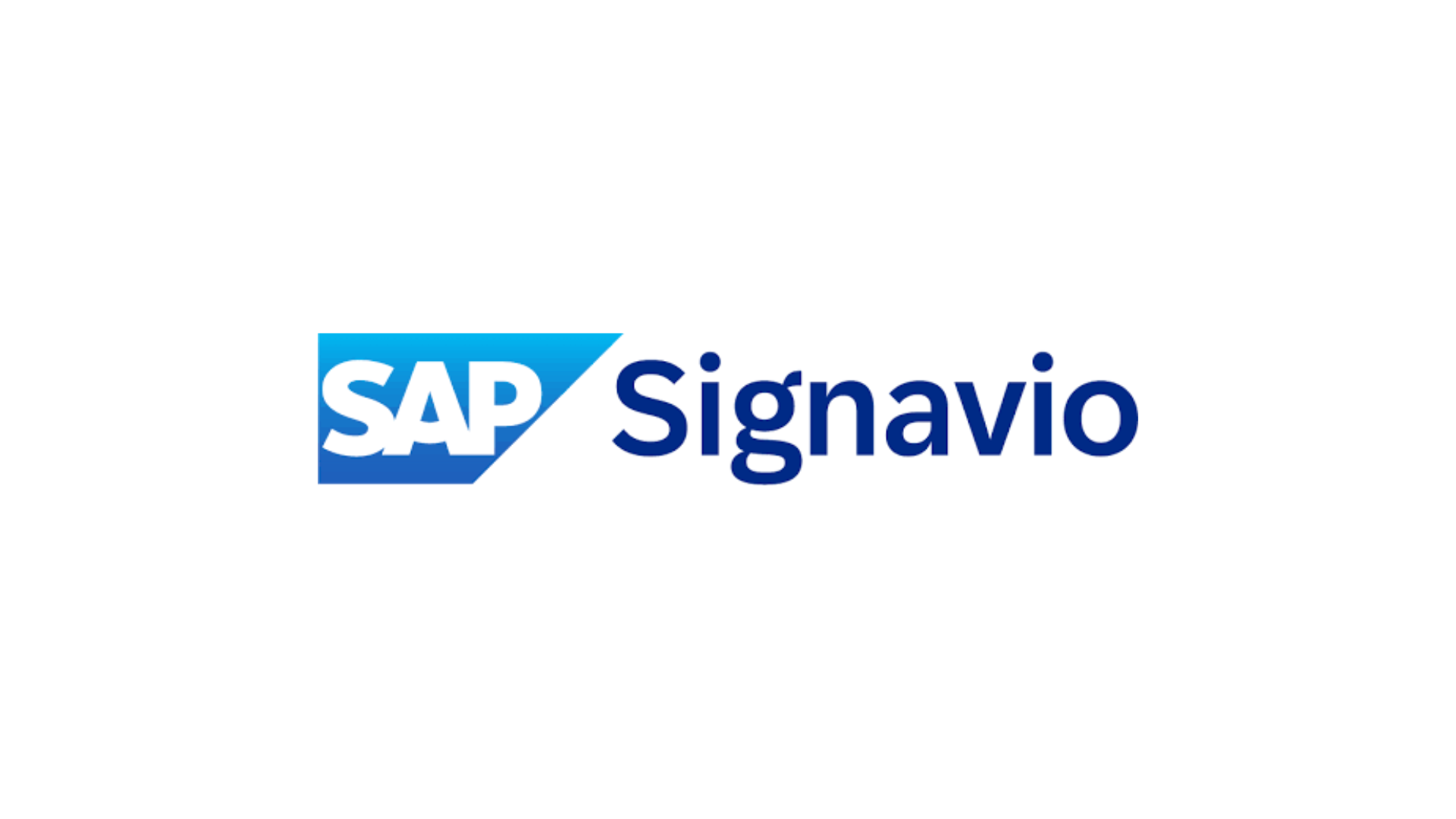
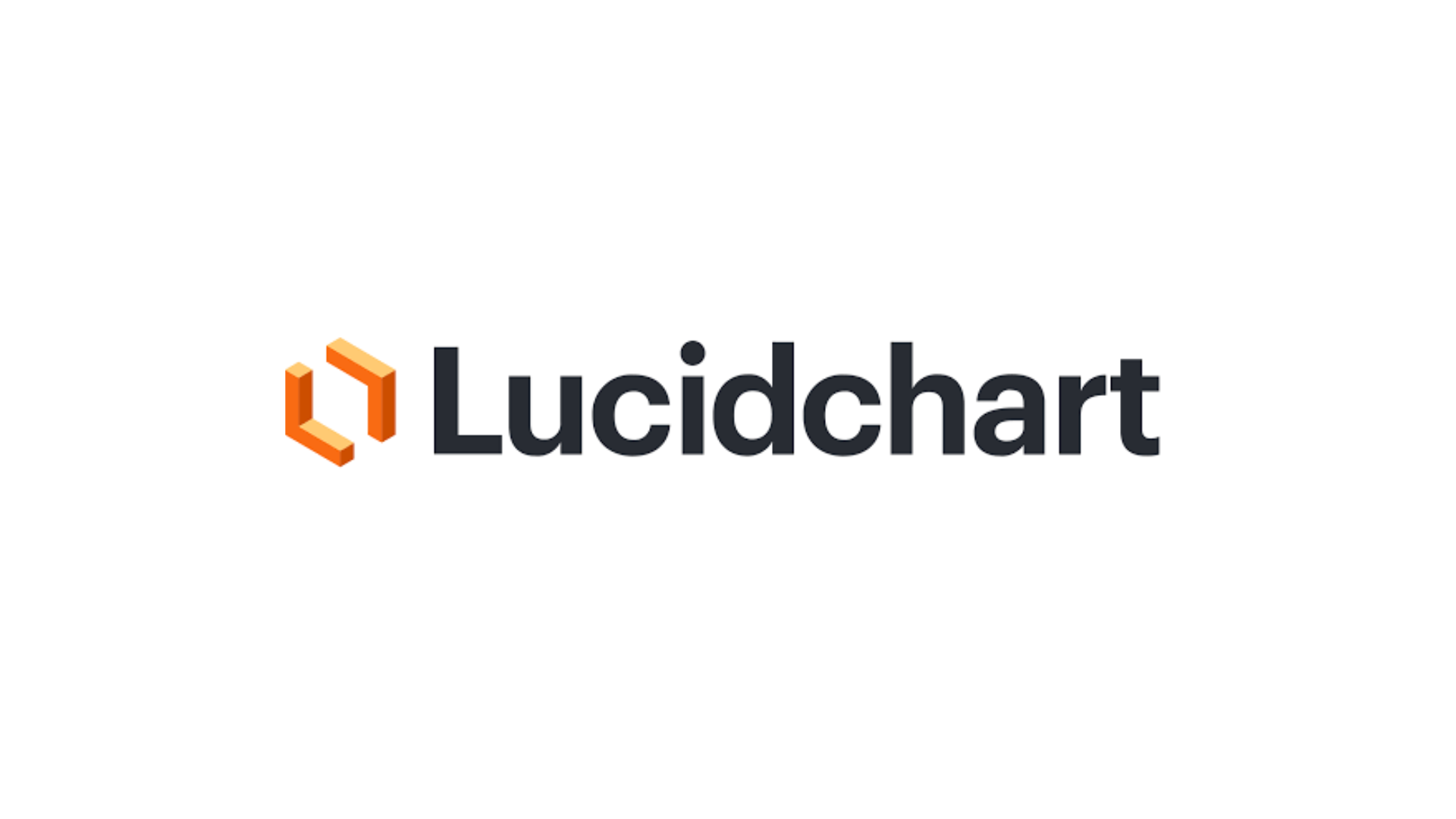

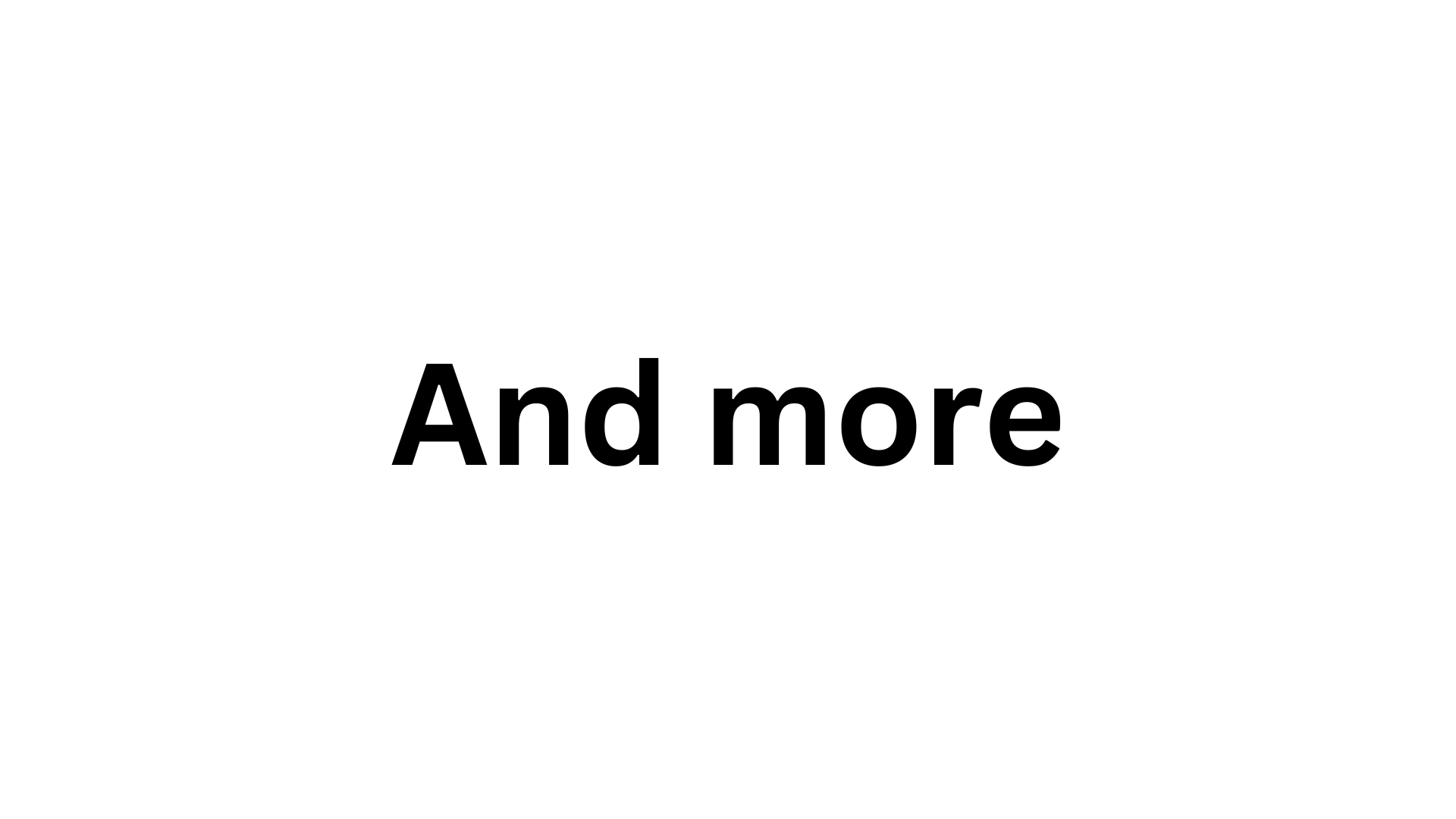
Our Process Mapping Methodology
It aims to provide a comprehensive and accurate representation of your business processes, preparing them for technology implementation such as ERP systems. We use a multi-level approach to ensure that we capture both the high-level flow and the detailed workings of your processes.
Understanding your business: We begin by engaging with your leadership team to gain a deep understanding of your business goals, key processes, and strategic vision. This initial phase helps us identify areas where process mapping can add value and align with your broader technology needs.
Level 1 Mapping for Alignment: Using diagraming tools, we create high level diagrams that offer an overview of your end-to-end processes. These diagrams capture the main phases and interactions without getting into the finer details, making them ideal for initial discussions with stakeholders and ensuring alignment on the overall structure before diving deeper.
Detailed Mapping for Insights: After establishing the high-level view, we transition to more detailed mapping, breaking down the broader steps into sub-processes and specific tasks. This level of detail is essential for understanding how each element of the process functions and how it contributes to the overall workflow. This stage is particularly important in preparing your processes for ERP or other technology implementations, ensuring that every aspect is clearly defined and optimised for system integration.
Assessing data for further analysis: As part of our detailed mapping, we assess the availability and quality of your existing process data. If sufficient and reliable data is available, we may recommend incorporating process mining techniques. Process mining allows us to validate whether the documented processes match real-world execution and to identify additional pain points or inefficiencies that might affect technology integration. This ensures that the process maps are not just theoretical but reflect the true operational flow.
Preparing for future state (To-Be) Design: The ultimate goal of our mapping process is to set the stage for designing your future state, making your processes ready for technology implementation, such as ERP systems. Our detailed maps highlight areas that need adjustment or optimisation to align with best practices for digital transformation. By focusing on the suitability for technology, we ensure that your mapped processes are not just improved but fully prepared for integration with new systems.
The Benefits
Tailored Insights for Technology Readiness
Our approach ensures that your processes are mapped with the end goal of technology implementation, specifically targeting ERP readiness.
Comprehensive and Multi-Level Views
We provide visual clarity at multiple levels, from high-level overviews to detailed task flows, catering to the needs of all stakeholders.
Stakeholder Engagement and Buy-In
Our collaborative mapping approach engages your team, creating a shared understanding of the processes and fostering support for future changes.
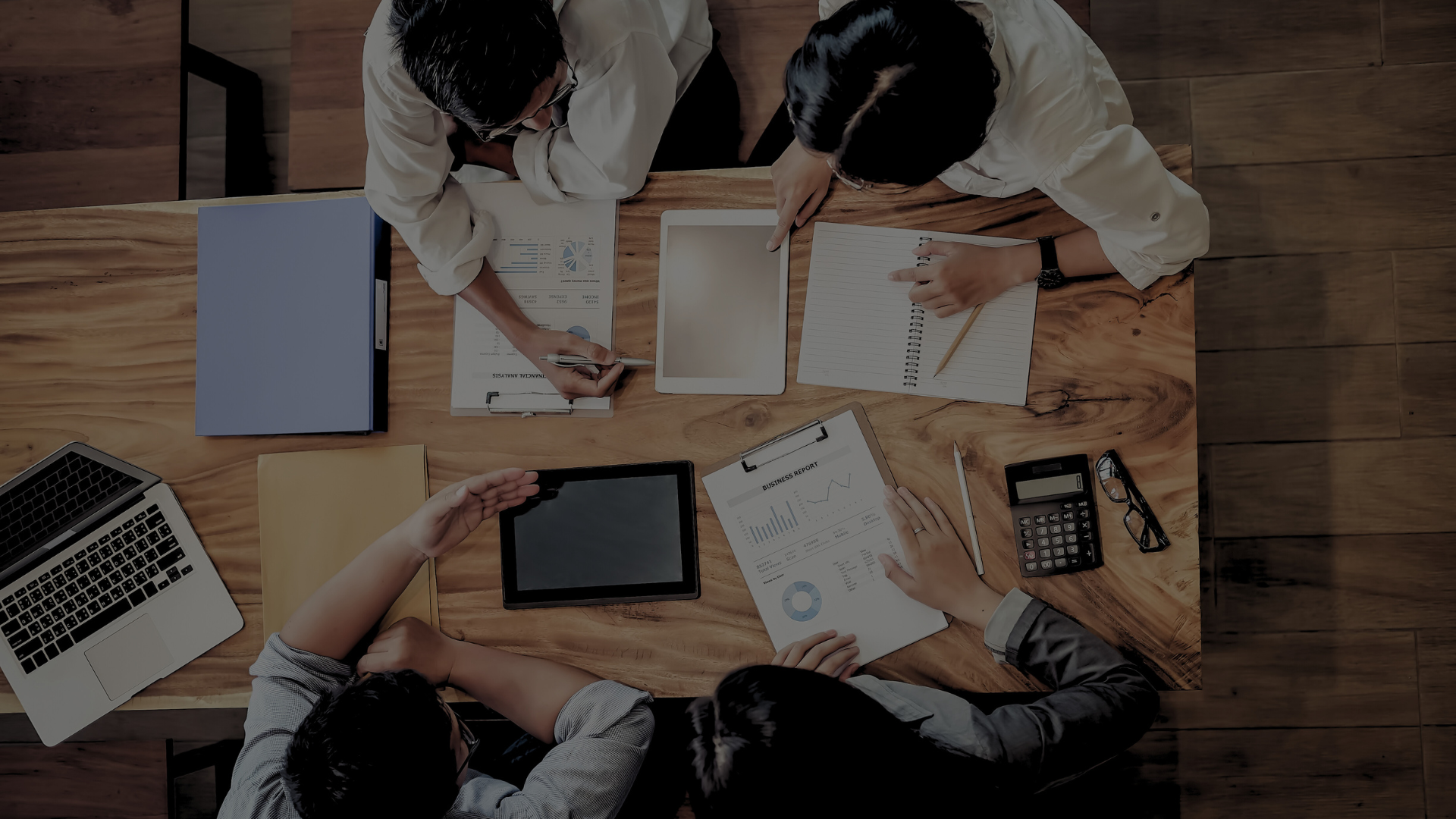